How Does the Pellet Manufacturing Machine Work
Pellet Manufacturing Machine Working Principle Overview
Speaking of pellet manufacturing machine working principle, we could say that the main component for working is composed of a flat die steel mould and a unit (2-4) of rollers with groove which can rotate flexibly. The raw material falls into the roller clearance from the top to bottom. After being pressed into the die hole by the rotary roller, it is formed into long cylinders, and cut into pellets with uniform size. The transmission mode have three kinds including driving roller, driving flat die and double driving.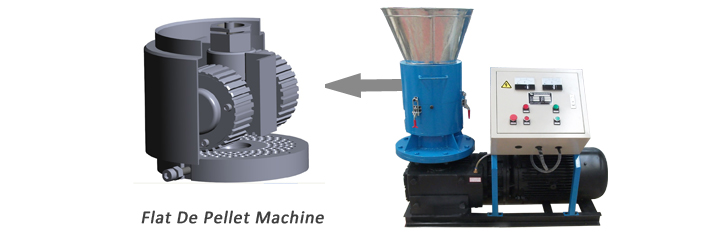
How Does the Popular Type Pellet Machine Work?
Flat die pellet manufacturing machine is designed with the features of simple structure, low cost and easy operation, suitable for pressing the fiber material. When pressing the raw material, due to the difference between the inner line speed of the flat die, resulting the difference of the centrifugal force on the raw material from the die, making the load is uneven. Therefore, the flat die diameter had better not be very large, or it will affect the final product uniformity.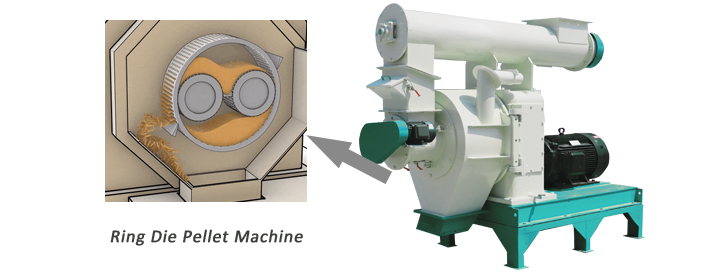
For the ring die pellet manufacturing machine, its working principle is based on a multi-hole cylinder, rotating by conveying. In the pelleting chamber are 2-4 freely rotating or driven rotating roller with grooves. When the raw material enters the die hole, it is pressed into the working room by rotating roller, inserted into the die hole, extruded through the die hole, and cut into cylindrical pellet by cutter.
How Does Other Types of Pellet Manufacturing Equipment Work?
- Functional pellet manufacturing equipment mainly uses mechanical crushing, mixing, pelleting and rubbing for reacting heat, to gelatinize the starch of the raw material, meanwhile using the moisture inside of raw material to make the feed pellet has high plasticity, thus better for operation of forming, drying and cutting.
- Soft pellet manufacturing machine is suitable for producing the raw material whose moisture content is in 20%-30%. The silage can be easily produced into thick liquid or made into pellet mixed with powder materials. Generally, the pellet is produced meanwhile being fed to the animals. If necessary, the pellet need to be dried before packing. The soft pellet manufacturing machine is designed with three types including screw type, impeller type and roller type. Among them, the screw type is the most common one, is mainly composed with cylinder, screw, die hole etc.
- Feed extruder mainly consists of feeding screw, debugging stirrer, extruding pelleting chamber, pellet cutter and power transmission etc. some simple structure is composed of cricket and sleeve etc. The working principle of the feed extruder is that the screw rotates at high speed in the sleeve, which produces squeezing and friction, thus increasing the temperature and pressure in sleeve (the temperature gets to 15CTC, and the pressure gets to 30-100kg/cm2), when the raw material is extruded out through the die hole, the temperature and pressure is decreased rapidly. Under the effect of temperature and pressure difference, the moisture in the feed evaporates fast, making the volume expand suddenly, thus the feed becomes into porous texture, and the moisture content reduces to 6%-9%.