Care and Maintenance of Briquette Machine Spare Parts
Anyone who have used briquette machine knows that the correct care and maintenance can not only prolong the machine lifetime but also improve the quality and output of the wood charcoal briquette. The propeller, sleeve and heating ring of briquette machine are the most wearable parts on the briquette machine, which is directly related to the normal continuous operation of the machine and the quality of the produced charcoal. Let's talk about the repair and requirements of the wearing parts on the
briquette making machine.
Briquette Machine Spare Part: Propeller
It is required that the size should be reasonable, while the texture is not the most important, because it is not itself that is subject to wear during work, but the part that is manually repaired. When repairing the thruster, wear-resistant electrodes with a diameter of more than 5.0mm should be used for one-time completion. After natural cooling, it will be polished according to the specified size, so that the surface is smooth.
-
The detailed operation is as followed:
If the propeller of the stick making machine is found to be worn, the propeller needs to be repaired. For the screw auger, it should be removed to be carefully inspected. If the bevel on the front end has severe groove marks or pits, and the elevation angle decreases, then it must be welded for repairing with using the special alloy electrode equipped in the screw propeller of the briquette machine strictly following the welding requirement. We need to preheat the surfacing of the propeller end to a temperature of about 200 degrees.
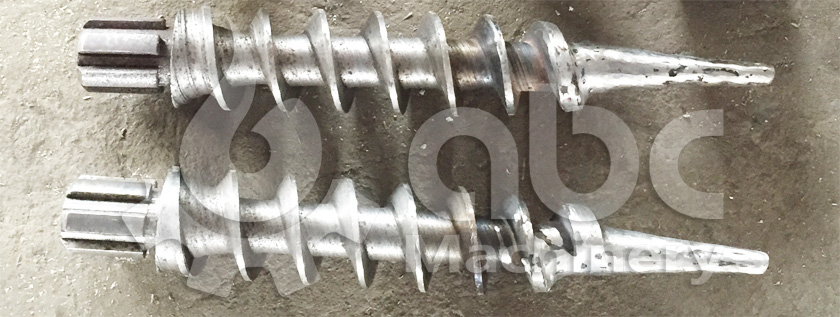
The welding part of the propeller surface need to be heated to 200℃. The welding electrode is made of wear-resistant electrode. The welding thickness exceeds the required thickness of 1-2mm. After welding, the insertion depth is more than three leads for cooling. When the temperature decreases under 50℃, take off the three leads, and then grind it on silicon wheels. Pay attention that the repaired propeller should be protected from collision and knock, and place it carefully. Additionally, using the repair technology of the briquette machine is the most critical, but also a step that the operator do not know. Use the special wear-resistant electrode to bead weld layer and layer according to the wear pattern of front corner of thruster end. For each surfacing layer, the slag must be removed before welding the second layer. After that, insert the welded part into dry quicklime or plant ash, and after the depth is more than three leads, start to cool. Take off it when the temperature decreases to 50℃, grind it on green silicon carbide wheels, during which do not use excessive force or local overheating, and strictly cool with water or other liquids.
Briquette Machine Spare Part: Briquette Machine Sleeve
Two aspects are required: reasonable size and wear-resistant. The wear degree of the sleeve is much less than that of the propeller, and a good sleeve life can reach about 3,000 hours. During production, the wear degree should be checked regularly. If there is a large pit spot, replace it immediately, otherwise it will cause poor quality or no rod at all.
GEMCO possesses strong technical force and strong production and development team, launching more cost-effective briquette machine and accessories to meet the requirements of our customers through our independently developed innovative technology, combining with advanced technology at home and abroad. For various models and specifications of the rod-making machine body, rod-making machine propeller, heating ring, forming cylinder, we have rich processing experience to ensure reliable quality and accurate size.